The AGO Film Processor: Hands Off, Spot On...
- Olly
- Mar 25
- 7 min read
Updated: Mar 29
When the AGO Film Processor first started making the rounds online, I was intrigued. I'd been developing black and white film at home using the Ilford standard inversion method, and whilst I had some experience with C41 too, keeping the temperature stable — even with a sous-vide setup — was always a bit of a balancing act. The idea of a compact, hands-free rotary processor with smart time compensation? That was enough to pique my interest.
I shoot and develop film regularly, but in a tiny space — the corner of our dining room — so I’m always looking for gear that makes the process easier without demanding more space. The AGO ticked all the right boxes. I ordered mine from First Call Photographic, and I’ve been using it consistently ever since.
First Impressions of the AGO Film Processor
My first reaction on unboxing the AGO was relief — it really is compact. I’d already seen a couple of videos on YouTube, so I had an idea of the size, and it matched expectations perfectly. No unnecessary bulk. No wasted space.
Some folks online had mentioned it being a bit noisy, but I found the sound totally manageable. Not silent, but nowhere near distracting — it doesn’t drown out my smart speaker or interfere with music whilst I’m working.
The build quality is solid. There are no weird gaps or weak points in the casing, and it forms a nice tight seal with the Paterson tank. It even comes with a two-reel tank, reels, and a pre-drilled funnel. There’s also a handy template if you want to customise your own funnel.


First Run — Fomapan & 510 Pyro
For my first test, I loaded a roll of Fomapan 400 into my Nikon F100 — a camera I trust to nail exposure, so I’d know any issues in the negatives were down to development, not the shooting.
I used 510 Pyro from Zone Imaging Lab and adjusted the development time from 9 minutes (standard inversion method) to 7 minutes and 40 seconds, to account for the 15% reduction typically recommended for rotary processing. I also ran it at 20°C, slightly cooler than the usual 21°C for rotary work.
I wasn’t nervous exactly — this was a test roll, after all — but I was genuinely pleased with the results. Clean, consistent negatives with no signs of uneven development. And using less chemistry thanks to the horizontal orientation of the tank? Even better.
Standout Rolls So Far
Since then, the AGO has developed:
15 rolls of 135 B&W
2 rolls of 135 colour
3 rolls of 120 B&W
1 roll of 120 colour
14 sheets of 4x5 B&W
And I’ve only charged it once since I got it at the start of January 2025.
Some standout results include:
Ilford Delta 100 in bright sunlight at St Annes beach huts, shot on a Rollei 35B
Ilford HP5 Plus at the West Lancashire Light Railway, with some great frames of the loco “Sybil”. (You can see my large medium and format results from their first photo day back in September 2024 here)
Fomapan 100 in 4x5, paired with a red filter — classic skies and bold contrast
Kodak Ektar 100 in ADOX C-TEC C41, shot in Llandudno — the colours were just gorgeous, with Ektar’s signature ochre warmth
My Setup: Small-Space, Big Workflow
My entire developing setup lives in the dining room — on a about 1ft by 3ft surface. I use a 12L water tank and a sous-vide for heating chemicals, with a bucket on the floor for drainage and a tea towel for drips.
The AGO fits in beautifully here. It’s compact, clean, and completely hands-off during operation, so whilst it’s running a step, I can wash out the previous jug, clean up, or sort through negs. Once the process finishes, I dry films from the shower curtain rail, or use 3D-printed drying racks for 4x5 sheets.
Switching between B&W and colour? I just run a 5-minute pre-wash to flush out stabiliser and Aldi washing-up liquid (yes, that’s my PhotoFlo alternative!).

The Greatness of Time Compensation
The AGO Film Processor’s biggest strength — and what really sets it apart from traditional rotary systems — is its built-in time compensation system.
Most home developers know the pain of chasing perfect temperatures, especially for colour processes like C41 or E6. Typically, colour development requires tight control at 38°C, and even a degree or two off can ruin your results. That means constant thermometer checks, hot water baths, and stress.
AGO does things differently.
How It Works
Inside the AGO is a temperature sensor that sits against the development tank. It reads the temperature of the chemistry (indirectly), and automatically adjusts the development time to compensate — using chemical-specific algorithms and published time/temperature data.
It supports major chemical kits, including:
Black & White: Ilford chart-based adjustment
C41: Tetenal, Cinestill, ADOX, Bellini, Arista
E6 & ECN-2: Supported with dedicated compensation graphs
This means you can dev film and AGO will simply extend the time to match. No panic. No scrambling. My dining room in Winter is only around 15–17°C so the tank loses temperature over the time taken to develop but the Ago compensates for this and still gives perfect results!
Whilst it doesn’t heat your chemicals, but it makes imprecise temps a non-issue. I've seen a lot of people whinging about this on social media (mainly Reddit!) so thought I'd clarify!

Why It Works for Me
Saves time — no standing over the tank
Uses less chemistry — tanks lie flat
Extremely consistent results
Battery life is excellent
Makes C41 surprisingly easy, even in a room at 15–17°C
Compact — perfect for small-space developers like me
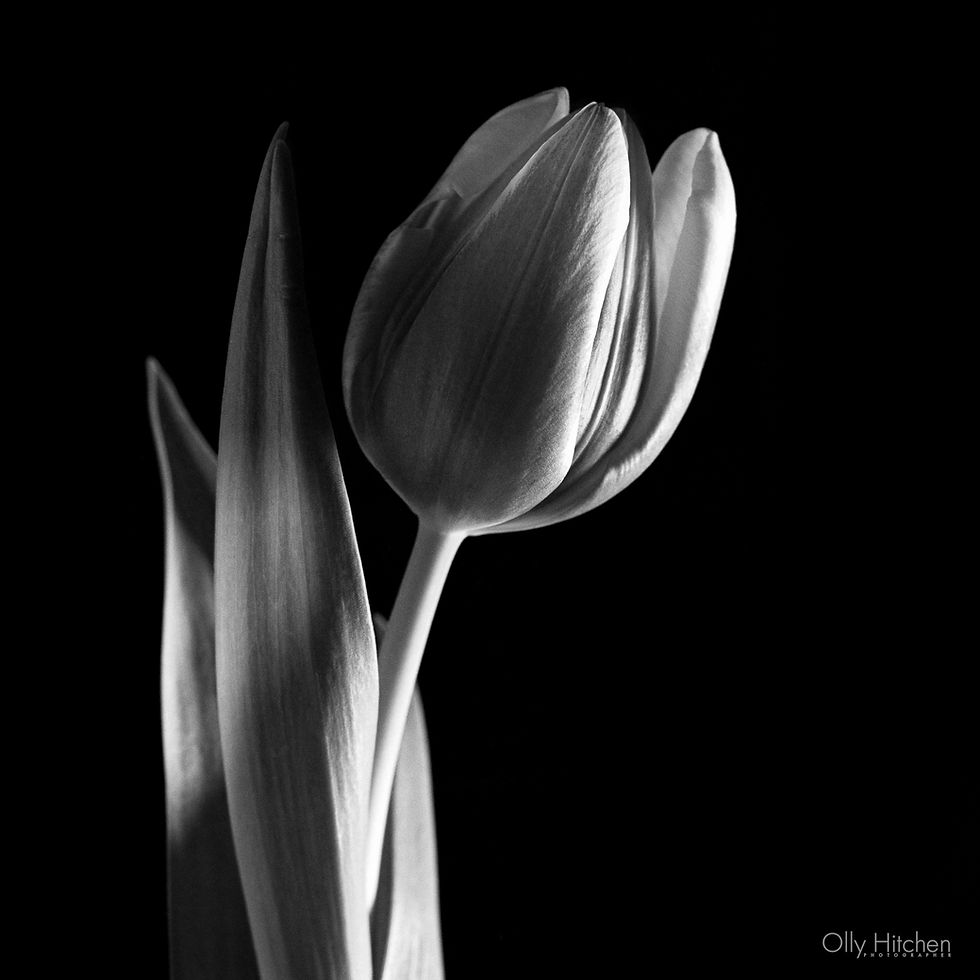
I wanted a way to economically develop 4x5 sheets without biolding out a darkroom (one day!) and the AGO offers a cheaper way to do this. I only have to use 450ml of developer for between 1-6 sheets of 4x5" as I use my MOD54 in it, which works a treat! Below are some shots taken in my Intrepid 4x5 Mk 5 and developed in the Ago Film Processor and my MOD 54.
What I’d Improve
The only thing I’d change is how custom programmes are edited. Right now, you can tweak existing steps on the AGO itself, but to build a full custom sequence you need to connect it via WiFi and use a desktop or phone browser.
I’ve tried editing on my iPhone 13 Mini, and whilst it technically works, the small screen makes it awkward. A tablet or laptop would be better. Honestly, I just forget to do it half the time — which probably says a lot about how important it is… or isn’t!
Technical Details & Other Useful Info
Minimum Chemistry Requirements for Rotational Agitation
Tank Size | No. of 135 Films | Minimum Volume (ml) |
1 Reel (small tank) | 1 | 250ml |
2 Reel (Universal) | 2 | 350ml |
3 Reel (Multi-reel 3) | 3 | 450ml |
5 Reel (Multi-reel 5) | 5 | 650ml |
8 Reel (Multi-reel 8) | 8 | 950ml |
Hardware Specs
Dimensions: 88 x 136 x 170 mm
Weight: 556g
Power: internal Li-ion batteries (USB-C charging)
Battery Life: One charge has lasted dozens of rolls!
Protection rating: IP56 (dust and splash resistant, so don't unk it when you clean it)
Features Snapshot
Pre-installed programmes for B&W, C41, E6, ECN-2
Fully customisable process sequences via WiFi
Agitation options: horizontal rotary or vertical stick
RA-4 and paper processing possible with special reels
Can operate whilst charging

Who Makes It? — Vintage Visual
The AGO is made by Vintage Visual, a small analog photography company based in Estonia. Their mission is to modernise film processing gear whilst keeping it accessible and compact for home and lab use. Their support and documentation are solid, and they maintain a support page and Discord/Facebook groups for updates, tips, and firmware downloads.
Would I Recommend It?
Absolutely. It’s not cheap, but it’s nowhere near Jobo or Filmomat prices either. I bought mine from First Call Photographic and found their customer service excellent.
I think the AGO is ideal for:
Home developers who want convenience and consistency
Space-limited users (seriously, it’s tiny)
Anyone nervous about colour processing
Small labs looking for a low-profile, programmable unit
One extra bonus? You can use it whilst it’s charging, though you’ll be tethered to a cable if you don't want to keep unplugging it and plugging it back in to keep it charging up.

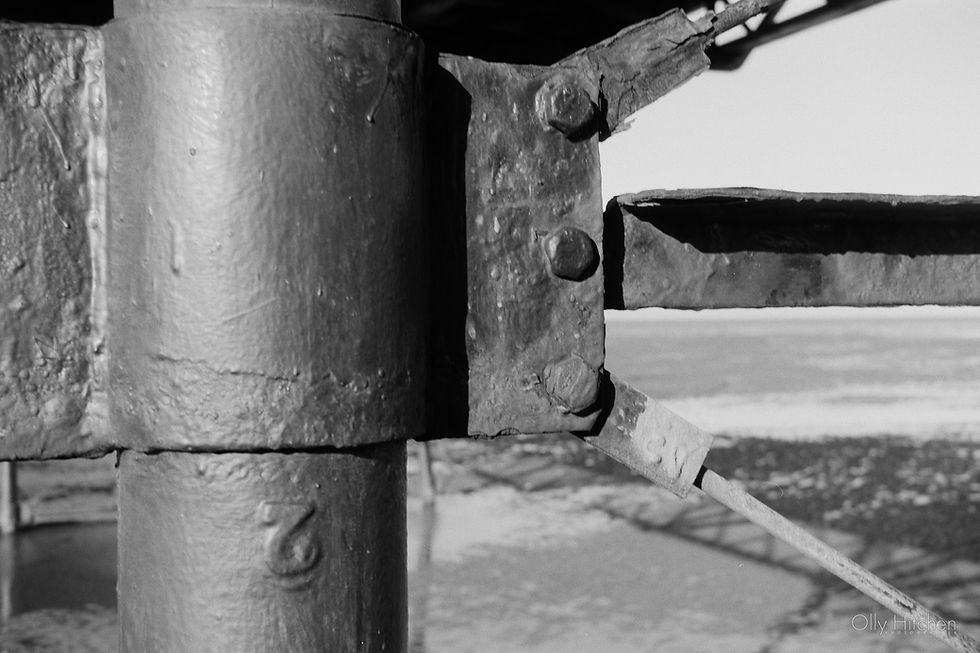
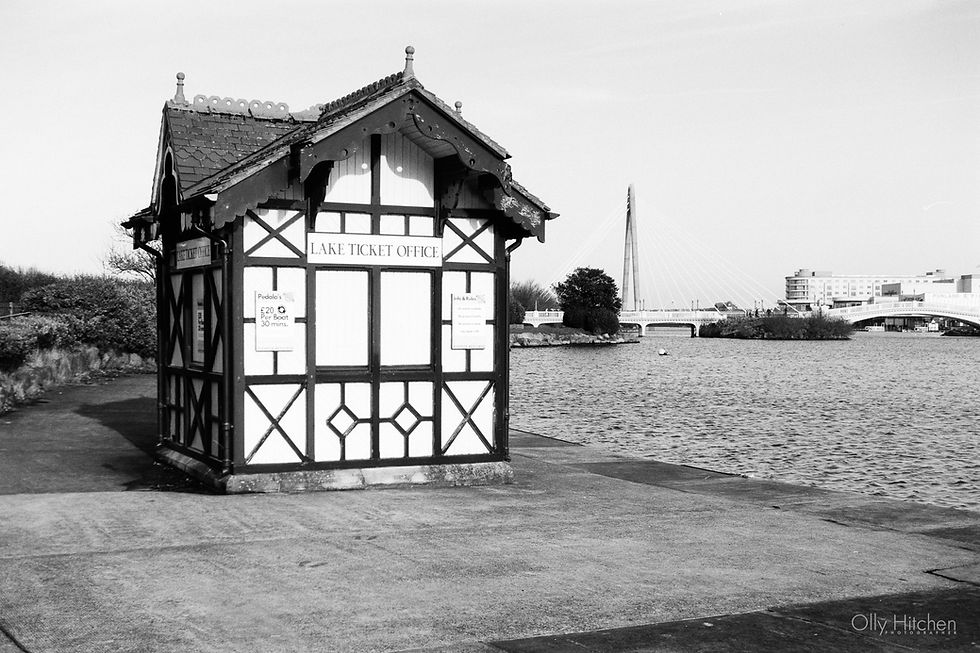
Final Thoughts
The AGO has become a key part of my workflow — compact, consistent, and clever. It’s helped me feel confident about colour again, and it makes developing film feel like less of a pain and more of a pleasure. Whether you're shooting 135, 120, or large format, and whether you're developing in Rodinal, Pyro, or C41 kits, the AGO slots neatly into a home setup and quietly gets on with the job.
If you’re looking to upgrade your home processing setup — and especially if space is at a premium — it’s well worth considering.
Definitely five stars from me.
Next are some examples of Ketmere 400 shot at 800 in my Voightlander Vito B at Chester Zoo, and Liverpool Cathedral on HP5 shot at 1600 in my Nikon F100
Finally, below is a small gallery of some shots taken in my Rollei 35B around Rydal Water on 12th March 2025 on Kodak Pro Image 100. Again, developed in the AGO Film Processor using the Adox C-tec 41 Kit.
Thanks for reading, hope you found it useful and good light!
Olly
PS: Don't forget you can find me on instagram here, or on Flickr here (where I post most many more photographs). Alternatively if you're feeling generous you can buy me a brew or help contribute to my film costs using the Ko-Fi link below!
Thanks!
Yorumlar